Teknogrout 350 Flowable Grout Mortar Without Shrinkage
Product description
It is a cement-based, one-component, self-levelling, flowable, one-component, non-shrinking, self-leveling mortar with high adherence and strength.
Usage areas
• In interior and exterior applications,
• Fixing steel columns and poles,
• Under all kinds of industrial machine beds,
• In engineering structures such as subways, highways, dams,
• In repair, repair and reinforcement projects where reinforced concrete curtains join with beams,
• It is used in the combination of prefabricated elements.
Features and Advantages
• It is an easy to use material, it becomes ready by just adding water.
• Does not shrink, shows high fluidity.
• Does not decompose and water vomit
• Can be pumped or poured.
• Solvent does not contain asbestos.
• It is resistant to freezing and thawing.
• Application thickness is 10 - 75 mm.
• It adheres well to concrete, does not contain chloride.
Application Instructions
Surface Quality: Concrete and metal surfaces should be clean, smooth, solid, free from cement laitance and weakened parts, and free from all kinds of dust, oil, ice, dirt, rust, mold oil, detergent, etc. The tensile strength (pull off) of concrete should be higher than 1 MPa.
All molds must have sufficient strength, TEKNOIL mold oil must be applied and insulated to prevent leaks. Insulation can be done by using TEKNOPOLIDERZ 1K under the formwork, around it and at the joints. Whether the mold is leakproof or not can be checked with pre-wetting water. During the grouting process, a suitable hopper/hopper should be made on one side of the mold to ensure a continuous grout height of 150 - 200 mm.
Surface Preparation: It should be prepared by cleaning with appropriate mechanical surface preparation techniques such as high pressure water jet, roughening, sandblasting. Absorbent surfaces should be pre-wetted, but no puddles should remain.
Mixing: 25 kg of powder material is poured onto 3.0 - 4.0 liters of water. These rates given may vary according to the air temperature. The mortar is mixed with a 400 - 600 rpm mixer for about 3 minutes until a homogeneous and lump-free consistency is obtained. After resting for 2 minutes, the material that is mixed again for 30 seconds becomes ready for use.
The prepared mixture should be placed in its place within 20 - 25 minutes depending on the air temperature and the amount of water. TEKNOGROUT 350 should be poured from one side to fill the bottom of the cavities that are surrounded and covered on four sides. Thus, it prevents the formation of gaps by throwing the air out. It can be pushed from one side with a long piece of iron during casting to accelerate the flow.
The casting thickness should be between 10 - 75 mm as the layer thickness at a time. It is recommended to make a preliminary trial if it is to be used in filling cylindrical small diameter anchors.
In applications thicker than 75 mm, 30% of the material can be added with 5 - 12 mm diameter aggregate.
Aggregate addition is done in two ways.
• The aggregate is added into the mortar. This process is continued for 3-5 minutes until a homogeneous mixture is obtained.
• Aggregate is poured or laid on the application floor. Then the mixture is poured onto the prepared TEKNOGROUT 350. The self-leveling mortar also allows us to obtain a high-strength concrete by wrapping around the entire aggregate.
Application Notes / Limitations
• It should be protected from sun, rain and frost for the first 3 hours in outdoor applications.
• Reaction times in cement based products are affected by ambient and ground temperatures. Reaction times are shortened in hot environments and longer in cold environments.
• Hot mixing water should be used in cold environments.
• In hot environments, cold mixing water should be used.
• During the application of the product, work clothes in accordance with the rules of work and worker health should be worn, and appropriate glasses and masks should be used.
• Do not use for patch-shaped surface repair works.
• Do not use a vibrator.
• Do not apply when there is a risk of frost.
• Do the pouring or pumping operation from one direction only.
• For best results, it is recommended to condition the material between (+)5°C and (+)25°C before use.
• After the application, it should be protected against adverse weather conditions such as direct sunlight, strong wind, high air temperature (over +35°C), rain and frost.
• Equipment should be cleaned with water immediately after the application, before it hardens. After the product hardens, it should be cleaned by mechanical methods.
Country / Region | Adana / Turkey | Main Products | Chemicals | Year Established | 2010 | Production Area | 5600 m2 | Main Markets | North America, Europe |
Business Type | Manufacturer, Trading Company | Trademarks | Ayks Chemical |
Total Employees | 10-40 People | Port | Mersin | Certification | ISO 22000 |
Material | Chemical |
Packaging | Insulated Polystyrene Box |
Production Equipment | Machine |
FAQ
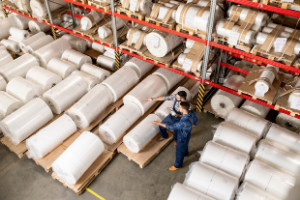

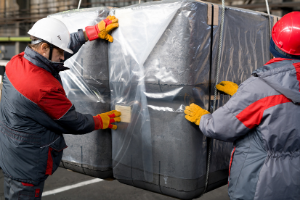

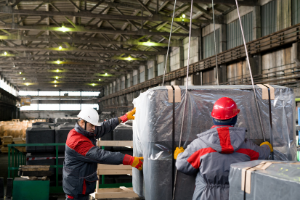
